Mantenimiento Proactivo
- Ángel J. Aranda Carmona
- 28 may 2017
- 4 Min. de lectura
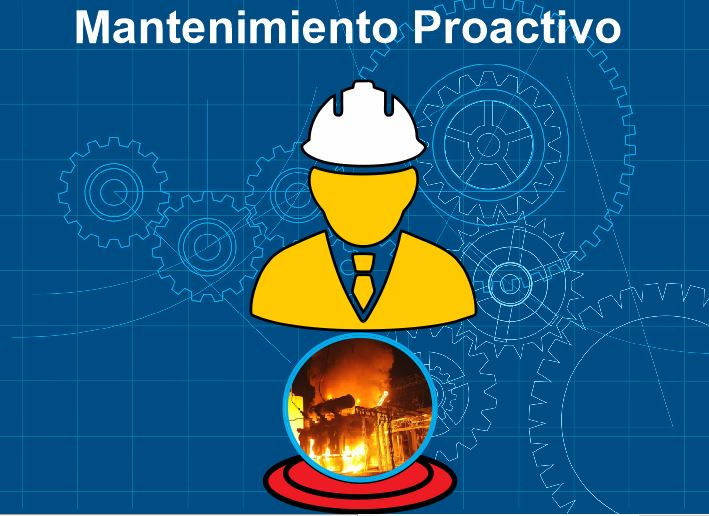
Antes de iniciar ¿Se han preguntado cuanto de los gastos fijos y variables de la organización se van al área de mantenimiento? ¿Cuánto tiempo del mantenimiento es correctivo? ¿Se presentan fallas recurrentes en la empresa?
El no tener una respuesta clara a estas preguntas implica una falta de control en el proceso de mantenimiento, esto se ve reflejado en los costos de la empresa y por lo tanto en una pérdida de ingresos.
El actual entorno económico busca que cada vez sean más eficientes los procesos industriales, los cuales están ligados a los objetivos estratégicos de rentabilidad y competitividad de las empresas. Para poder cumplir con estas metas cada vez son más las organizaciones que utilizan estrategias más adecuadas de gestión del mantenimiento, las cuales han ido evolucionando, profesionalizando las actividades que, en un principio dependían de la capacidad del técnico en cambiar los equipos fallados o realizar composturas en el menor tiempo posible, lo que representa una visión muy corta del mantenimiento; bajo esquemas de productividad esa función debe depender de alguien con conocimiento no sólo técnico, sino con visión de ingeniería del mantenimiento, conocer el activo, sus modos de falla, desempeño, vida útil, riesgos, entre otros factores que permitirán entender cuáles son las condiciones bajo las cuales se debe realizar el mantenimiento, en que tiempos y que actividades, con el fin de reducir tiempos de atención y gastos innecesarios.
Bajo esa premisa, se presenta el mantenimiento proactivo como una herramienta útil para cumplir con estos propósitos.
El Mantenimiento Proactivo es una técnica enfocada en la identificación y corrección de las causas que originan las fallas en equipos, componentes e instalaciones, esta técnica implementa soluciones que atacan la causa de los problemas, no los efectos, buscando eliminar la recurrencia de estas fallas. Una aplicación exitosa de esta metodología permite generar ahorros de más del 50% del gasto en mantenimiento, lo que se refleja directamente en la productividad, reducción de tiempos de mantenimiento y por lo tanto en la rentabilidad de la organización.
Este método se considera el más eficaz para la reducción de riesgos, mejorando la confiabilidad y garantizar la rentabilidad ya realiza acciones concretas que reducen costos en fallas, tiempo de paros y aumento de la vida útil de los activos.
Desde el punto de vista del mantenimiento a equipo eléctrico, presentamos algunos casos en los cuales se observa el que se debe realizar y los beneficios de esto.
En el caso de transformadores eléctricos de mediana y alta tensión, los equipos más costosos e importante de una subestación y en la que de presentarse una falla de estos activos representa un gasto por falta de producción y por el remplazo del mismo, genera pérdidas de por lo menos unos miles de dólares. ¿Sabemos cuáles son las principales causales de falla? De a acuerdo la investigación de William H. Bartley del Hartford Steam Boiler Inspection & Insurance Co., entre 1991 y el 2010, entre la humedad y malas conexiones se tiene un 10% de las fallas.

¿Qué acciones de mantenimiento proactivo podemos realizar para evitar estas fallas? Sólo la limpieza, evitar el ingreso de humedad y las inspecciones rutinarias de las conexiones eléctricas podrían reducir el riesgo en un 10%, permitiendo que estos factores dejen de ser una fuente recurrente de daños en equipos eléctricos.
En el caso de los cables de potencia, una de las principales causas de falla es en los conectores y empalmes, ¿y por qué fallas estas secciones en especial? Es claro que en esos puntos existe una distribución diferente del campo eléctrico, y por lo tanto una concentración de esfuerzos en el aislamiento, pero si el diseño de las terminales es adecuado, el armado de estos elementos es el problema, la razón, la falta de cuidados y la contaminación. Al ser elemento de alta tensión en un circuito homogéneo, cualquier elemento extraño con características conductoras, influirá en que se presente concentración de campo eléctrico y por lo tanto descargas parciales, que en tiempos relativamente cortos puede provocar fallas críticas a tierra o entre fases de los cables.
La solución, capacitar al personal y una adecuada serie de pruebas de puesta en servicio para eliminar uno delos principales causales de fallas en cableado.
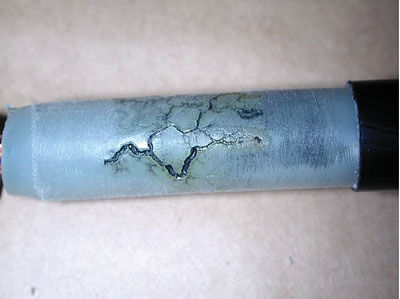
En motores eléctricos, por ejemplo, las fallas por sobrecalentamiento del aislamiento son una causa importante de fallas, el aislamiento de los motores modernos ya es principalmente clase F y clase H, lo que indica que pueden soportar temperaturas de hasta 150°C y 180 °C, pero que el aislamiento tenga esas propiedades no significa que deban operar continuamente a esta temperatura, se tiene evidencia que aún estos aislamientos operando a temperaturas superiores a los 100°C comienzan a envejecer rápidamente llegando a un punto en el que el daño es irreversible, Entonces ¿por qué se operan a estas temperaturas? Las sobre cargas, una falta de enfriamiento o ventilación adecuado son las causas de una potencial falla en el aislamiento.

Por esta razón, ¿cuáles son las acciones de mantenimiento proactivo que debemos realizar para evitar el daño térmico en el aislamiento de los motores? Muy sencillo, antes que nada, elegir adecuadamente el motor, para que no trabaje con sobre cargas, ya teniendo en operación el equipo, realizar monitoreo continuo de la temperatura de los devanados, eliminando los factores que puedan incrementar la temperatura de operación de los mismos y de esta manera incrementar su vida útil.
Con esos casos se puede observar que acciones sencillas y económicas que implican el conocimiento del activo y por lo tanto sus factores de riesgo, se pueden generar ahorros importantes en la organización, reduciendo la tasa de fallas, tiempo de mantenimiento y por lo tanto es posible concentrar los esfuerzos en factores más complejos que puedan representar también un riesgo para la salud de los activos eléctricos.
Komentarji